Transform your factory with connectivity
This IDC InfoBrief highlights the importance of connectivity to support and drive successful smart manufacturing initiatives and enable integration in the factory and across value chains. In this document, you’ll find key reasons why connectivity decisions should be strategically evaluated, and outlines the benefits of information integration.
In this guide, we’ll highlight key reasons as to why connectivity decisions should be strategically evaluated and outline the benefits of information integration. We’ll also provide a practical overview of the key use cases that can be enabled by a strategically-driven connectivity approach.
The manufacturing industry is exposed to a variety of challenges
Manufacturing operations are the beating heart of the manufacturing industry. Manufacturers continue to invest in smart manufacturing technologies to improve their factory operations, to maximise yield from existing production capabilities, and develop next-generation production capabilities necessary to thrive in this volatile and uncertain world.
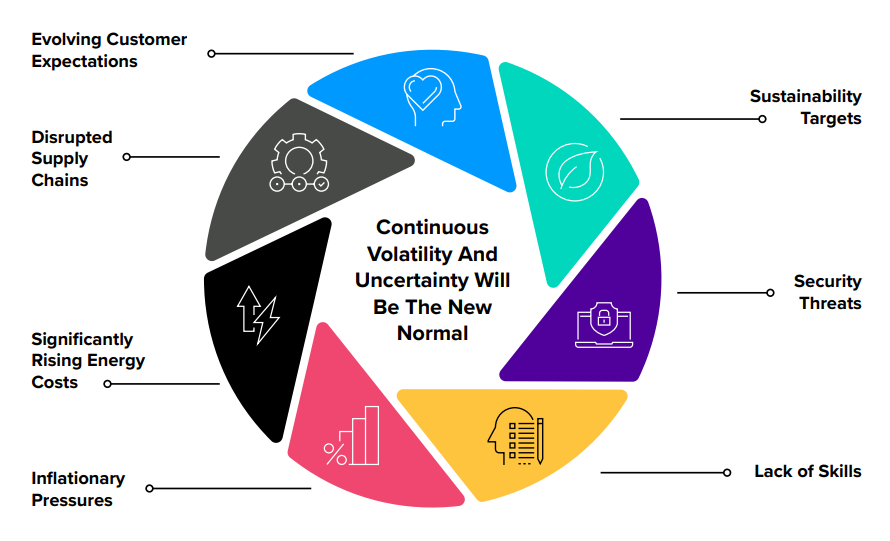
Smart manufacturing is all about digitally connecting the manufacturing processes to drive operational innovation.
As companies consider digital transformation to build long-term resilience in manufacturing, the core enabler of this transformation is asset instrumentation and integration, including smart tools (IT/OT convergence, edge, controls standardisation, IIoT, networking).
Digital technologies including edge and cloud architectures enable the Factory’s BIG transformation
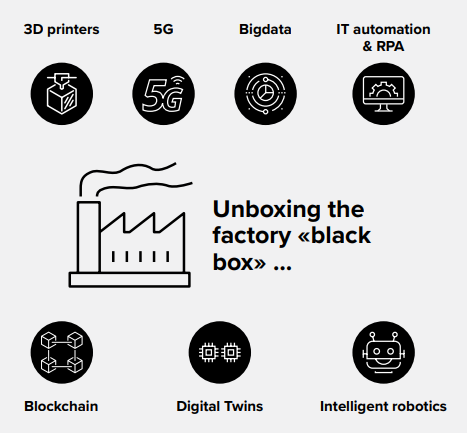
For manufacturers, managing operational complexities has been the core focus. As manufacturers strive to improve operational efficiencies and drive faster product innovations, they also need to speed up their decision making to stay ahead of the competition.
Manufacturing organisations are integrating new technologies, including AI, machine learning, cloud and analytics to transform their factory processes. And with today’s data-driven manufacturing, edge-to-edge cloud architectures are central in creating, analysing, and distributing data from the shop floor to the top floor to allow for better decision making. Integrating IT and operations technology (OT) environments is an essential first step in ensuring seamless and consistent information flows for improved decision making.
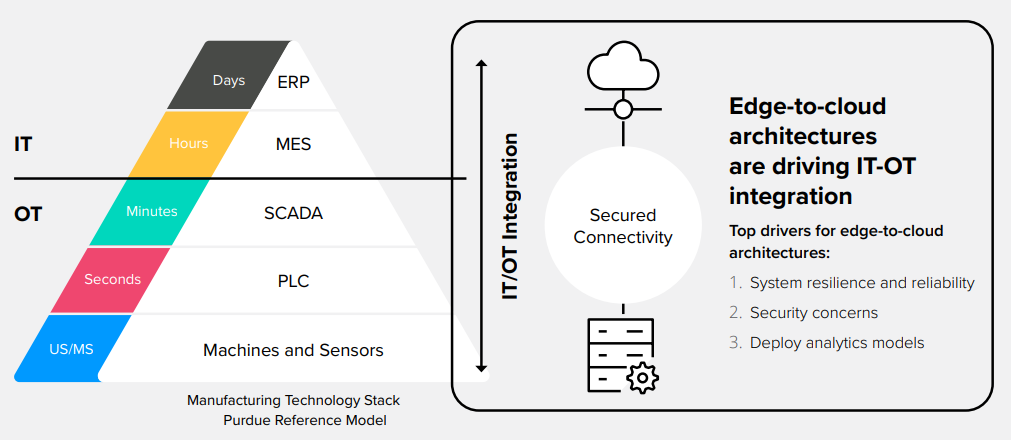
Machine instrumentation continues to expand along with factory connectivity, resulting in unprecendented amounts of data
Vast volumes of data are gathered, moved, processed, and actioned in a distributed environment, to/from/between clouds. Industrial companies need to address their network strategies to bridge user, compute and store, handline massive data and distributed IT workloads to get to the ‘next practices’.
- High bandwidth connectivity is essential to move large volumes of data around key points of the environment quickly and reliably
- 5G technologies have the power to seamlessly enable denser connectivity, higher data capacity and lower latency
5G is bringing new connectivity features to support the ‘smart manufacturing’ journey
5G, in addition to providing local and wide-area site connectivity, has the potential to additionally provide local and wide-area connectivity for personnel, AGV and IoT devices with ultra-low latency and massive connection density where required. Also, guaranteed network performance on 5G, enabled by network splicing.
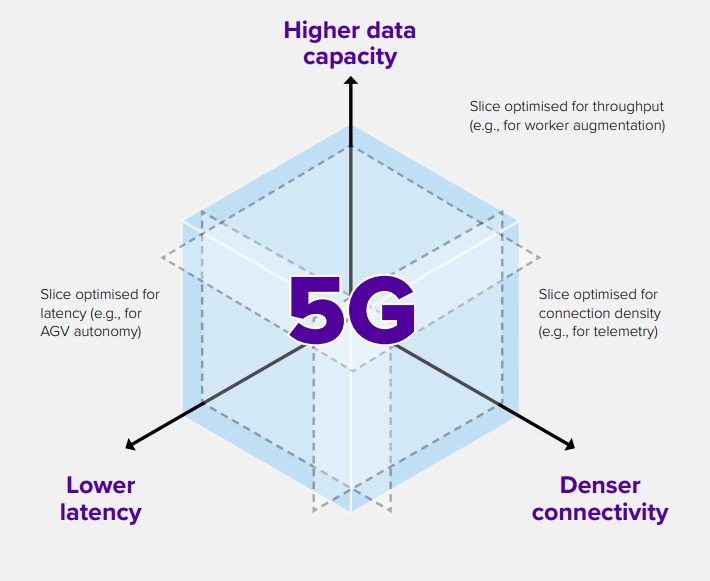
5G is enabling the smart manufacturing journey:
- Production connectivity – product tracking can achieve larger scale because of the number of connected endpoints that 5G cell sites can support
- Process optimisation – 5G can connect a feedback loop that continuously gathers large quantities of data about process activity and analyses it to identify areas that can be improved
- Remote/centralised operation – the ultra-low latency use case of 5G makes it a highly responsive network, responsive enough that taking an action at one end of a connection can produce an action at the other end that is effectively instantaneous
- Worker augmentation – 5G can provide support by carrying high-definition multimedia information to AR-equipped “augmented” workers
Connectivity is the centrepiece of technology (r)evolution
We are witnessing a “new wave” of operational technology investments centred around information integration and IT components, such as cloud, analytics, and connectivity – this signals a change from the past where when the focus was on OT hardware.
There’s a clear pattern emerging when evaluating companies’ investment strategies – planned investments focus on building cloud-based operational data layer enabling analytics while resting on solid connectivity and security components.
A solid multi-cloud strategy will be key for factories to transform operational data into actionable information in a cost effective way. In fact, AI-ML, business analytics, and other tools are only efficient if they can be processed quickly. Hence, reliable, secure and high-performance connectivity infrastructure (both on-prem and in the cloud) is paramount to guaranteeing a successful transition to smart manufacturing.
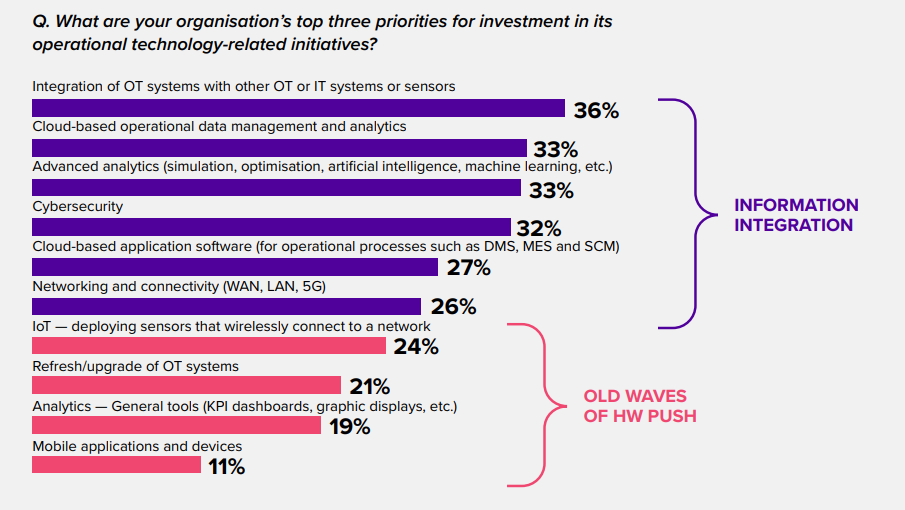
Operations workload distribution is rapidly changing as cloud workloads are projected to grow at a much higher pace
The act of moving/storing/processing huge amounts of data (several TB or PB) needs careful analysis of data size, hosting locations, and movement/transfer. For example, the network and connectivity capabilities should suffice to connect at scale, where and when a company needs it. And it is vital to ensure data sovereignity and security ‘in-flight’ – i.e. when critical data is moved (for storing/processing) back and forth across locations.
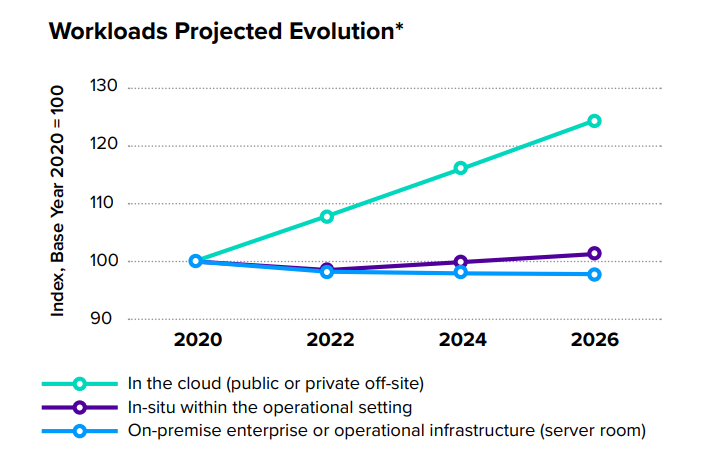
Connectivity is vital in driving this information integration from shop floor to top floor and across companies
As value chains are turning into value networks, industry ecosystems are becoming a renewed way to generate value. A core pillar for this is data exchange, but above all this requires trust, followed by appropriate platforms, infrastructures and applications that support relevant use cases.
Manufacturing companies must share information with each other in the ecosystem (suppliers, partners and customers) to ensure process coordination and efficiency at the most granular level.
Reaping the rewards of information integration: manufacturers can move on from “best practices” to “next practices”
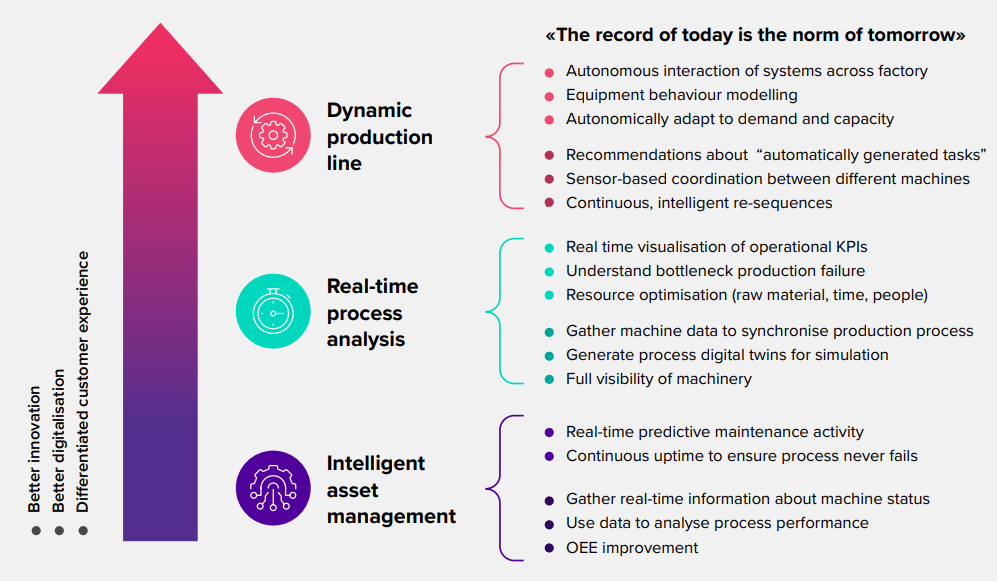
It’s not just about optimising existing processes but transforming the way factories are run, creating new compelling use cases around asset management and analytics, and ultimately running processes more efficiently. Companies that have made the journey are already reaping rewards:
Question: Please estimate the impact that IT/OT convergence has on:
Unscheduled asset downtime or outages (reduction) | 3% – 15% |
Throughput or productivity | 6% – 18% |
Scrap, defects, laboratory failures (reduction) | 1.5% – 13% |
Energy cost per unit (reduction) | 4% – 15% |
OT security incidents (reduction) | 3% – 15.5% |
Environment, health & safety incidents (reduction) | 5.5% – 16.5% |
Labour costs (reduction) | 1.5% – 12% |
Speed of changeovers | 2.5% – 14% |
Inventory turnover or supply chain visibility | 7% – 18% |
The strategic relevance of connectivity projects is directly correlated with smart manufacturing maturity
In order to progress through the stages, companies should focus not on the technology per se, but on how technology enables information management. It is important to note that equipment and technology do not make as much difference as the ability to use information effectively to support business processes.
IDC Smart Manufacturing Maturity Scope, 2022
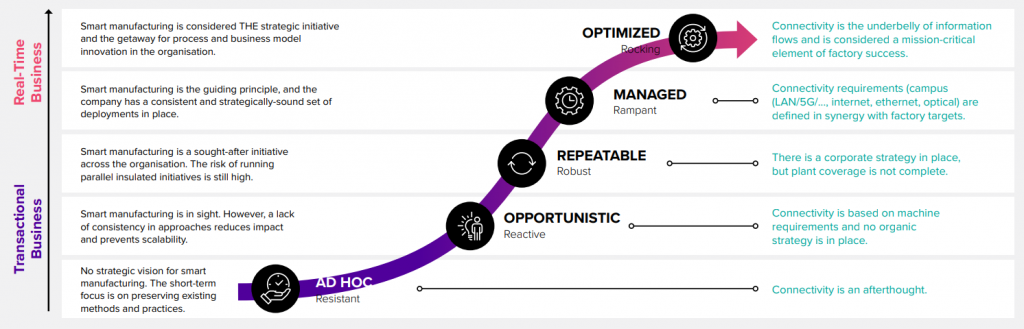
Connectivity is a key element in bringing together all technology opportunities that transformation is carrying
There are different use cases, each demanding different locations of workloads, including M2M, edge and cloud – these locations must be managed in a concerted way to create the best value for the business. WAN and LAN connectivity are central through this.
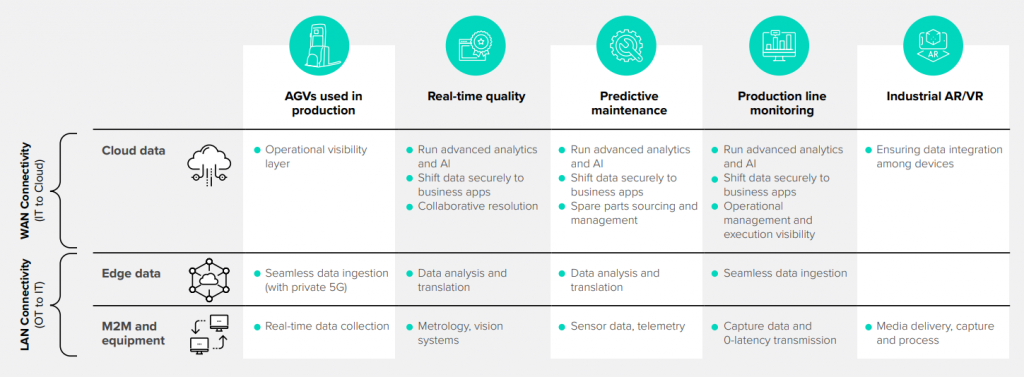
Solving integration problems exceeds companies’ internal capabilities and requires a holistic approach to industry transformation
Several manufacturers struggle to manage their industrial connectivity without external support. There are still a lot of barriers to overcome, and this requires active support from external companies and partners.
Question: Please select the top 3 barriers to IT/OT integration in your organisation:
Concerns about the security of integrating IT & OT systems | 42% |
A lack of expertise or staffing capability to accomplish integration | 34% |
Technology issues/non-compatible legacy applications | 33% |
Too many decision makers/organisational complexity | 33% |
A lack of budget | 31% |
Not enough familiarity with the concept of IT & OT integration | 27% |
Not high enough priority/lack of management buy-in | 23% |
Lack of business case for the initiative | 23% |
Question: How much technical support does the team that manages OT need to receive in the following technology activities (Share of support needed)
Operations cybersecurity | 51% |
Industrial networking | 44% |
Advanced analytics and machine learning | 42% |
Data management including tagging and semantics | 38% |
Application development in low-code environments | 38% |
Several public initiatives are being launched to stimulate different building blocks of smart manufacturing across Europe
As connectivity becomes the core enabler of industrial transformation, several initiatives are taking place at the regional level to support companies in their journeys and enable even the smaller manufacturers to benefit from ecosystem transformation
To develop 5G Supply Chain Diversification Strategy in the UK
UK Telecoms Innovation Network Competition (UKTIN), aimed at supporting the telecoms industry to navigate the UK’s telecoms R&D ecosystem and drive the development of open networks, will grant a consortium funding of up to £10 million to set up a public-facing body that supports the goals of the government’s 5G Supply Chain Diversification Strategy.
To develop 5G ecosystem between France & Germany
Both France and Germany have industrial capabilities and relationships. The Franco-German joint call for projects on industrial 5G has two key objectives: to encourage their industrial companies to deploy use cases for 5G private networks and adopt the technology within their factories; and to encourage development of their 5G solutions for the manufacturing sector.
To develop AI ecosystem between France & Germany
France and Germany have signed a joint declaration of intent to create a “Research and Innovation Network in Artificial Intelligence”. It includes Smart Industry & Production Technologies as one of the application areas.
IDC Guidance
Pressured by accelerated disruptions, manufacturers are on the verge of a revolution in the way that they use information. Every worker needs to access information through the cloud, connected equipment, and even wearables. Every single piece of information needs to be delivered to multiple audiences inside and outside the organisation. And the more information around, the more it will be requested from shop floor users and other business units. In this journey, connectivity plays a central role. IDC provides the following guidance to manufacturing end users:
- Establish your starting point by assessing you current factory floor technologies footprint and evaluating your relative maturity in connectivity adoption, which needs to be strategic and not an afterthought.
- Review your connectivity foundation to make sure it’s ready to support increasing amounts of digitally-enabled assets and processes. As manufacturers become increasingly sophisticated in their use of technology, what is ‘nice to have’ increasingly becomes the ‘must have’.
- Leverage existing connectivity opportunities (sensors, mobile, RFID), starting from quick wins as a launchpad to develop the business case for larger investments.
- Cultivate your existing talent and ensure that IT and line of business are collaborating as true partners in the selection and implementation of new technologies.
- Work with external providers, across system integration, software, networking, and equipment worlds to accelerate your IT capabilities and serve the lines of businesses. External resources and expertise can help you move quickly and effectively, which is essential in today’s global marketplace.
Colt’s world-class network enables your digital transformation
In partnership with Ciena, Colt’s global optical netwwork footprint is operating at mulit-terabit scale using modern 800Gpbs technology to meet the massive data mobility requirements of next-generation applications and services. Our commitment is to provide agility in high-bandwidth services, supporting datacentre, digital and cloud transformation capabilities for manufacturing industries.
To deliver proofs of concept and customer-ready solutions such as AI, predictive maintenance and cybersecurity, Colt and IBM have also launched a joint lab environment to address the challenges of industry 4.0 in the manufacturing value chain:
- Seamless integration of IBM’s hybrid cloud and AI technologies, including IBM Cloud Satellite and the IBM Maximo Application
- An environment for our joint customers to optimise manufacturing operations while enabling the convergence of IT and OT with Colt distributed edge
